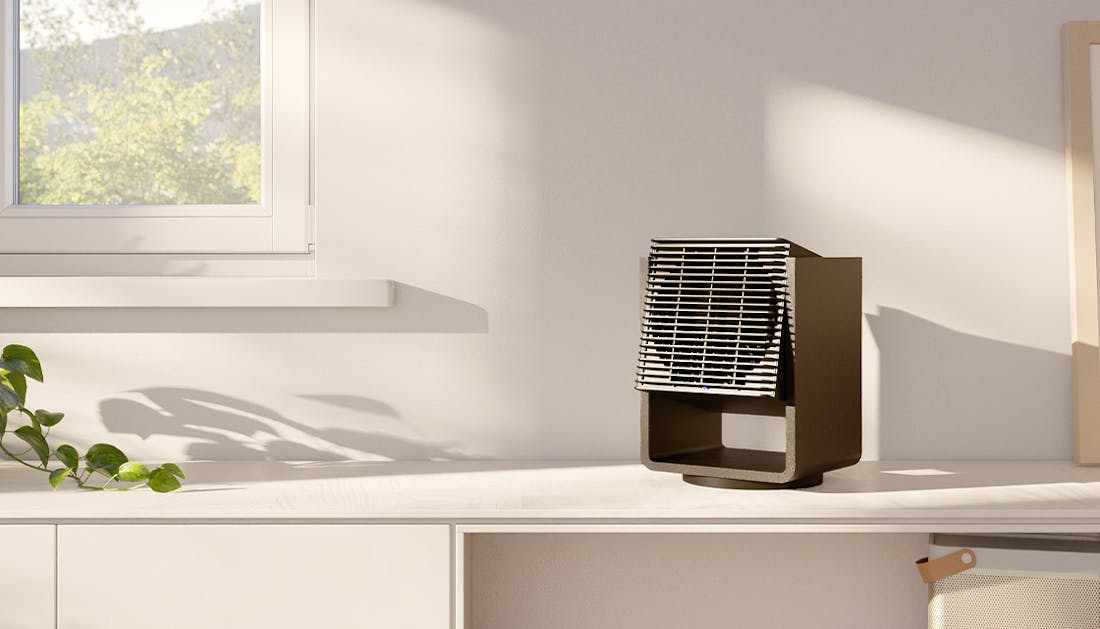
Usha Müller , 14 juillet 2025
Régler la température de l'air
Product development and optimisation at Stadler Form: A case study with Alex
It is a long journey from the initial idea to the finished product at Stadler Form. Market analysis, design development, and prototype construction are all important steps in creating innovative new products. Read on to find out how this process worked for the AlexAlex fan heater, who came up with the idea for this product, and what technical challenges arose during its development.
Find out in this article
- From idea to development
- Design development as a central element
- Technical specifications
- Ongoing product optimisation
From idea to development
The journey from the initial idea to the finished product is exciting and multifaceted. Product ideas usually arise from a personal need and are brought to us by our CEO and Head of Product Development, Martin Stadler, our Head of Production and Quality Control, Thomas Becker, or other Stadler Form employees. Ideas from employees across the company are also considered, as they provide creative impetus and innovative approaches. The designers' ideas are also taken into account, as their professional background gives them a different perspective and often brings different creative and functional aspects to the table. Customer feedback is also incorporated into the idea generation process to better understand the wishes and needs of the target group and optimise the device accordingly.
An initial idea is followed by thorough market research to identify demand and current trends. To better assess the market, existing devices from other brands are tested to analyse their strengths and weaknesses. These findings are incorporated into the development of new products to create innovative and competitive products.
According to CEO Martin Stadler, the idea for Alex came about as follows: «Thomas Becker and I discovered a 2-in-1 device like this on the market and thought the idea of combining a heater with a fan was really innovative.» The idea to develop the best 2-in-1 device, a fan heater and fan, was born. ‘Our goal was to develop a fan that could also heat. This is very innovative and not often found on the market. And fan heaters that also function as fans often produce very little wind. Our combination device was to be a fully functional device in both categories,’ Martin Stadler continues.
Once an initial idea has been developed, a clear definition of what the device is and what functions it should have is established – both from a technical perspective and in terms of user experience. The entire process is characterised by continuous exchange, analysis and innovation – always with the goal of developing a device that meets the needs of users and is successfully positioned on the market. The most important factors for Stadler Form are design, innovative functions, ease of use and energy efficiency.
Design development as a central element
Next, Martin Stadler decides which designer or design duo is best suited to create the new product. He selects from a small circle of Swiss designers with whom Stadler Form has been working for many years. Why did he choose Matti Walker as the designer for Alex? "It was a gut feeling." Thanks to Martin Stadler's many years of experience and his personal relationships with the designers, he usually makes decisions based on his gut feeling or the specific expertise of the designers. The product idea, including the technical requirements, is explained to the designer. In a personal meeting on site, the product development team discusses the requirements and ideas with the designer.
The designer or designer duo then creates initial designs on paper to visualise various creative approaches. Together, they select a promising design that best suits the product idea and Stadler Form as a company. The designer visualises the product using CAD (computer-aided design) to create as realistic an image of the new product as possible. If the computer visualisation is not sufficient, the designer also creates a model using a 3D printer or makes it by hand to get a realistic idea and make any necessary adjustments.
The finished designs are then presented by the designer at the Stadler Form office in Zug, where they are discussed and evaluated together with Martin Stadler, Thomas Becker and the product development team. This exchange is crucial, as everyone involved is encouraged to contribute their input and concerns to further optimise the design and ensure that it meets the desired requirements.
Once the design has been finalised, it must be registered with the IGE, the Swiss Federal Institute of Intellectual Property, as quickly as possible. The IGE legally secures the design so that it is protected and no copies can be made or must be removed from the market. Alex's design has also been registered.
According to Martin Stadler, developing Alex's design was anything but easy: "Alex was technically very challenging. We originally wanted to design him as a ceramic fan heater and fan. However, it quickly became clear that this idea was not feasible because too little air flowed through the device and Alex would therefore not be a fully functional fan. So, we built in a kind of door so that the ceramic heating plates could be folded to the side when Alex was to be used as a fan. Unfortunately, the idea was anything but practical: too loud, too complicated and, in the end, too expensive to produce. That's why we abandoned the ceramic heater idea and opted for a circular wire heater with wire loops." Due to his complex functionality, Alex had to go through a few extra rounds in the design process – around ten working prototypes were created before the design and technology were just right.
One of the biggest challenges in the design process was integrating the motor for horizontal oscillation into the narrow base. Alex has a lot of technology packed into a small device. «When Alex seemed to be finished, he was too bulky for us, so we challenged the factory again. The factory managed to reduce Alex by 1 centimeter on each side, making it the perfect device it is today», explains Martin Stadler, whose pride in the result of hard and sometimes tough work is clear to see.
This creative and intensive process makes design development a central element of product development. It is the only way to consistently create new and protected designs.
Technical specifications
With the idea and an initial design, product development moves on to one or more factories. The number of factories that receive the order to produce a prototype depends on the product in question. If, for example, a new fan is to be produced, the factory with which the best experience has been gained with fans in the past is selected. If, as in Alex's case, it is unclear which factory is suitable for the new product, factories are commissioned to develop a prototype. To this end, the design and user interface are described as accurately as possible to give the manufacturers a clear idea of what the final product should look like. The factories then communicate what is technically possible with the chosen design.
Daniel Zeder, Product Manager, explains the choice of factory as follows: "It is important that the factory has the relevant expertise and that the quality is right. We have long-standing partnerships with the factories that manufacture our products and are therefore able to assess which factory would be suitable for the new product. We also visit the factories several times a year and our on-site quality manager plays an important role in working with the manufacturers. We also listen to our gut feeling when it comes to who can best implement the product. And, of course, the price-performance ratio has to be right so that we can compete in the market. It's no use to us if we develop a product that is completely out of line with market expectations. Of course, quality comes at a price, but it must not exceed the budget.
A functional prototype is then produced to test its practical suitability. This is thoroughly tested in Switzerland and at the respective factory for functionality, appearance and noise emissions, among other things. This testing process is precisely documented with reports, images and videos. Once testing has been successful, a decision is made as to which factory will take over production. If the prototype meets the desired requirements, the mould for production is made and the first T1 sample is produced. Based on the test results, optimisations are implemented, for example on T2, T3 or further samples. Between the individual samples, the 3D model is used to see if and what adjustments are possible. It must be ensured that all applicable standards are met.
During the development of Alex, the team realised that the prototype was too loud. Wanting a quieter 2-in-1 device, Martin Stadler contacted the Institute of Mechanical and Energy Engineering (IME) at the HSLU, which specialises in fluid mechanics and numerical methods. The team led by Prof. Dr. Ernesto Casartelli took on the challenge. Using FFT analysis, the CAD image was analysed in software to identify where in the device the loud noises were coming from. They concluded that the fan blades needed to be enclosed by a ring to reduce the noise. Furthermore, the propeller, including the fan blades, had to be redesigned to minimise noise emissions. As a result, the team redesigned the propeller and created a prototype. After several tests and adjustments, Alex's current propeller was created.
The swivel function was also a major challenge for Alex, as the fan heater and fan had to swivel both horizontally and vertically. "Ensuring that the swivel function runs smoothly and quietly in a device that offers little space is a huge challenge. In Alex's case, the motor for horizontal oscillation is built into the U-shape, including the base. It was almost impossible, but we managed to integrate the technology successfully in the end, " explains Martin Stadler.
Ongoing product optimisation
Feedback from the market – from end customers, distributors, retailers and other partners – is taken very seriously. As the appliances from the Swiss market are tested and repaired at the in-house Stadler Form Service Centre in Zug, Switzerland, proximity to customers and appliances is always guaranteed. This enables a quick response to any challenges. If a technical issue is identified that is not working optimally, it can be improved immediately. When a product is optimised, it is carefully tested with the new features before the changes are integrated into the next production run. This ensures that our products always meet the highest quality and functional standards.
If you have questions related to indoor room climate, please get in touch with us. Or subscribe to our newsletter to regularly get informed about current topics regarding indoor climate, experience reports or Stadler Form insights.